先日は、デザイン画を中心に紹介しましたが、今回はその作製編です。
なお、作製したのは私ではなく加藤さんですので、あしからずw
-----------------------------------------
まず、全体の工程はこんな感じです。
![]()
初めに、硬質ウレタンの塊から、外形を切り出します。
![]()
![]()
このスピーカー、4つで1セットになっていて、
合体させると円柱状になり、運搬しやすい形になるのが特徴です。
つぎに、石膏型を作製します。
「お面」のように、一面づつ制作していくので、
「切り金(ひらひらした薄い板)」で境界を作ります。
![]()
ここに、石膏を吹き付けて(?)、型を作ります。
石膏型ができたら、硬質ウレタンの土台と分離させます。
![]()
石膏の形を整え、表面処理を行いFRP(繊維強化プラスチック)整形に適した下地を作ります。
この石膏に、樹脂や硬化剤などを含む「ゲル」を塗り(?)ます。
そこにガラスマットを貼り付けることで、FRPの層を作製します。
ちなみに、この工程を繰り返すことで、厚いFRPを形成することができます。本作品は厚さ4〜8mm程度だとか。
FRPを石膏から剥がし取り、表面を滑らかにします。
![]()
![]()
![]()
あとは、これらのFPR製パーツを接合し、塗装をすることで
SPの箱となります!
特に本作品は三脚で支持するので、重心バランスを考慮したうえで支持ポイントを探す必要があったとのことでした。
そして、出来上がった作品がこちら!!
![]()
![]()
![]()
![]()
![]()
市販品に引けを取らない、見事な作りですね!
特に、ユニットを保護する「ライン」は参考になりますね。スタイリッシュでありながら、機能性抜群な感じが漂っています。
ちなみに、アンプも本体内に格納できます。
![]()
スピーカーは、そのデザインが性能に直結するので、数あるインダストリアルデザインの中でも興味深い製品だといえますね。
加藤さんは今後イヤホンなどのデザインに携わりたいとおっしゃっており、今後が楽しみです!
なお、作製したのは私ではなく加藤さんですので、あしからずw
-----------------------------------------
まず、全体の工程はこんな感じです。

初めに、硬質ウレタンの塊から、外形を切り出します。
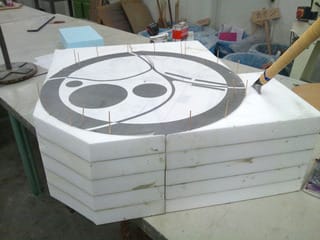

このスピーカー、4つで1セットになっていて、
合体させると円柱状になり、運搬しやすい形になるのが特徴です。
つぎに、石膏型を作製します。
「お面」のように、一面づつ制作していくので、
「切り金(ひらひらした薄い板)」で境界を作ります。

ここに、石膏を吹き付けて(?)、型を作ります。
石膏型ができたら、硬質ウレタンの土台と分離させます。

石膏の形を整え、表面処理を行いFRP(繊維強化プラスチック)整形に適した下地を作ります。
この石膏に、樹脂や硬化剤などを含む「ゲル」を塗り(?)ます。
そこにガラスマットを貼り付けることで、FRPの層を作製します。
ちなみに、この工程を繰り返すことで、厚いFRPを形成することができます。本作品は厚さ4〜8mm程度だとか。
FRPを石膏から剥がし取り、表面を滑らかにします。



あとは、これらのFPR製パーツを接合し、塗装をすることで
SPの箱となります!
特に本作品は三脚で支持するので、重心バランスを考慮したうえで支持ポイントを探す必要があったとのことでした。
そして、出来上がった作品がこちら!!




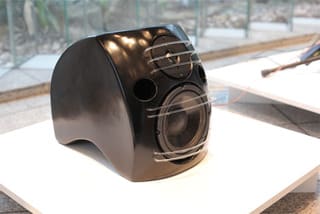
市販品に引けを取らない、見事な作りですね!
特に、ユニットを保護する「ライン」は参考になりますね。スタイリッシュでありながら、機能性抜群な感じが漂っています。
ちなみに、アンプも本体内に格納できます。

スピーカーは、そのデザインが性能に直結するので、数あるインダストリアルデザインの中でも興味深い製品だといえますね。
加藤さんは今後イヤホンなどのデザインに携わりたいとおっしゃっており、今後が楽しみです!